Lockout/tagout procedure (often labeled as “LOTO procedure” or “lockout/tagout”) is one of the top ten most frequently cited standards by the Occupation Safety and Health Administration (OSHA).
That means, LOTO standards compliance is often inspected and controlled by OSHA and eventually may result in hefty fines for companies that do not meet the policy.
And it’s not a surprise. Properly implemented lockout/tagout program can prevent many injuries, incidents, and even deaths occurring in workplaces.
So, what does the lockout/tagout program include and how to start with its implementation? We looked at the official materials from OSHA and CDC to bring a detailed overview to everyone interested in the topic.
What is a lockout/tagout procedure?
Lockout/tagout (LOTO) is a technique used to prevent energy from being released during the servicing of equipment. The procedure is executed in several steps in which an authorized employee ensures that equipment is properly shut down and any potentially dangerous stored energy is isolated and released prior to maintenance.
LOTO procedure also includes placing tags and locks on energy isolation devices (e.g., power switches, control valves) to prevent their unauthorized use during the servicing of a machine.
This process ensures that the equipment is shut down and inoperable until workers complete the planned action.
However, do not confuse lockout and tagout as performing a similar function. The lockout device stops employees from working on the equipment.
Meanwhile, the tagout tells them not to work on the machinery. In short, both are hardcore protection against unsafe equipment where the lockout device is the first layer, and the tagout device is the second.
When to use tags and when to use locks?
Locks are used when the equipment is required to be locked physically. It’s used as an energy-isolating device that turns off the energy source of the machine to secure the device in a safe position.
In the meantime, tags come perfectly handy where locks can’t physically lock out energy-isolation devices.
Along with that, they also provide crucial information like who approved the lockout, why it was approved, and also keep you up to date about the current status and time.
Colors of lockout locks and tags
Till now, OSHA has provided no standardized color-coding system for lockout locks and tags. However, there is a generally used system regarding the typical color codes:
- Red tag = Personal Danger Tag (PDT)
- Orange tag = group isolation or lockbox tag
- Yellow tag = Out of Service Tag (OOS)
- Blue tag = commissioning and test tag
- Red lock = used to lockout equipment during a maintenance procedure
- Orange lock = used to indicate that it is safe to perform service procedure
- Yellow lock = used to lockout equipment before servicing by an affected employee
- Blue lock = used in place of orange lock for lockboxes having 6+ isolation points
Guidelines & standards
The American National Standards Institute (ANSI) published its first-ever lockout/tagout practicing guidelines in 1982. The purpose was to deliver safety precautions needed when employees were doing maintenance of hazardous energy sources.
Then, in 1989 those guidelines became the Occupational Safety and Health Administration (OSHA) regulations. If we talk about the guidelines prescribed by OSHA, they cover all energy resources from mechanical to thermal, including electrical, hydraulic, pneumatic, and chemical. And these are crucial for the maintenance activities of manufacturing plants.
As far as LOTO is concerned, its name itself indicates that it used two approaches to ensure the safety of employees during maintenance activities.
These lockout and tagout procedures limit energy access to equipment and show warning signs to notify employees about upcoming hazards.
Who needs to comply with LOTO OSHA standards?
Generally, U.S. companies must meet Occupational Safety and Health Administration regulations. OSHA covers almost all private sector businesses within the 50 states and other territories of the U.S.
Employers need to make sure that workplaces have the appropriate safety precautions in place. They should also work on minimizing short- and long-term hazards that can threaten the physical and mental health of employees.
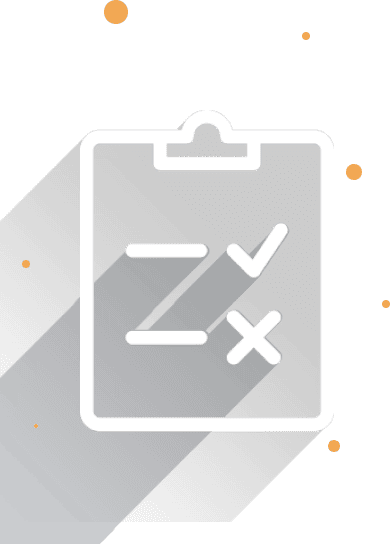
Possible Hazards Checklist
Download a free Possible Hazards Checklist template to significantly improve your workers’ safety by completing the hazard scans
Importance of LOTO
Safety practices in a plant’s operations are crucial to safeguard employees from avoidable harm. A shocking number of tragedies can occur while the maintenance procedure and LOTO implementation can ward off such tragedies efficiently. It basically blocks the energy sources of equipment from activating during maintenance to reduce the risk of injury.
Lockout procedures prevent equipment energy sources from activating when they should not, particularly during maintenance when employees are at risk of injury or death.
Effective lockout-tagout procedures also moderate downtime and protect costly equipment by ensuring it is shut down properly.
Hazardous risks that can be prevented
These are the three situations; workers are at risk of accidents.
- Maintenance procedures
- Cleaning Machinery
- Removing items stuck in machinery
These underlying situations require coworkers to work more closely with the moving parts on equipment. But, if any kind of mishandling occurs, there is a high risk of injuries.
With proper LOTO, here are some examples of incidents that can be averted:
- During maintenance or examination, getting suffocated if the machine starts moving or re-energizes
- Electrocution due to not cutting off the power supply ahead of the time
- Getting fractures or losing a limb due to moving parts of the machinery
- Getting the body part crushed under the moving machinery
- Third-degree or lethal burns because of pouring hot liquids or toxins that weren’t blocked during machine maintenance
Types of energies LOTO prevents
When you prepare the equipment for maintenance, often hazardous energies are released. These energies can be:
- Chemical
- Pneumatic
- Electrical
- Mechanical
- Hydraulic
- Thermal
For the workers, the energy sources in machines and equipment that count electrical, mechanical, hydraulic, pneumatic, chemical, thermal, or other sources are unsafe. If during the maintenance procedure there is an unexpected startup or release of stored energy, it can cause drastic effects or even the death of the workers.
10 steps to implement lockout/tagout (LOTO) procedure
Stage: Preparation of a lockout/tagout program
1. Develop and document machinery energy control procedures
To begin with a LOTO procedure, you need to identify devices and machinery to which hazardous energy control programs will apply. Document a step-by-step process for correct shutting down and restarting of this equipment, include its location and details that will help eliminate possible dangerous actions.
You should be as specific as possible in this step as the documentation will provide fundamental guidelines to authorized employees. Depending on the complexity of the equipment and its application, proper procedure documentation may vary from one to many pages.
OSHA explains what should be included in the documents as follows:
- A statement on how to use the procedures;
- Specific procedural steps to shut down, isolate, block, and secure machines;
- Specific steps designating the safe placement, removal, and transfer of lockout/tagout devices and identifying who has responsibility for the lockout/tagout devices; and
- Specific requirements for testing machines to determine and verify the effectiveness of lockout devices, tagout devices, and other energy-control measures.
2. Select and train employees authorized to use LOTO procedures
Every worker should have a clear understanding of when energy control procedures apply, but personnel who perform the maintenance should be also qualified to use the procedures. The authorized employees must be trained to understand the hazards and how to implement safety measures to mitigate risks.
Stage: LOTO application
3. Prepare for the machinery lockout/tagout
Before the actual shut down of machinery, authorized personnel have to notify all affected employees about planned maintenance or servicing, and that energy control procedures will be applied.
Provide exact information about the time and duration of the maintenance and update them if any changes were made during the process. This step is necessary to prevent unexpected attempts of equipment re-energization.
4. Shut down
In this step, an authorized employee will shut down the equipment using a standardized procedure (e.g., power switch) documented in the guidelines.
5. Isolation of energy sources
Workers then locate and isolate all energy sources of the equipment. This may include actions such as turning off power cables or shutting a valve.
6. Lock and tag placement
After full isolation of machinery from energy sources, authorized personnel attach lockout and tagout devices to parts that can be used for re-energization.
This can include electric breaker panels or control valves. The locks and tags are necessary to prevent manipulation of equipment from unauthorized employees.
Each individual authorized for locking or tagging a machine should use signed or person-specific locks or tags, so everyone knows who placed them.
A worker who places the devices should be also the only one allowed to remove them according to OSHA guidelines.
7. Stored energy release
Even after proper shutdown and equipment lockout procedures implementation, machines can possess safety risks because of the stored residual energy.
For example, spring tension, heated liquids, or venting gases could be accidentally released during maintenance and thus need to be handled beforehand. Workers should also secure all moving parts that posses safety hazards throughout the maintenance.
8. Energy isolation verification
In the last step before the maintenance itself, authorized personnel should inspect the proper application of the previous steps.
The machinery is shut down, all energy sources are isolated, locks and tags are in place, and residual energy is released. After the successful inspection, workers can proceed with maintenance.
Stage: LOTO removal
9. Equipment re-energization
After technicians complete the maintenance, an authorized employee verifies that all workers are aware of the planned re-energization and that they are positioned safely on the worksite.
It is also necessary to remove all tools and repair equipment. This process includes removing the tags and locks by the same person that placed them, and reenergizing the machine.
10. Procedure update
The best practice of the lockout/tagout procedure includes at least annual updates of the documentation and equipment inspections.
Make sure your guidelines are always up-to-date and follow the latest OSHA standards.
Bonus step:
Process standardization and Health & Safety assessment with mobile inspection software
Inspection software can automate various processes within the LOTO procedure thanks to checklists, mobile forms, inspection reports, or appointment management.
For example, authorized personnel can use mobile software throughout all the steps of shutting down and re-energization of equipment.
With a tailor-made lockout/tagout checklist, they can check if all necessary steps were completed correctly and in the right order.
Digitalization of these processes also enhances data collection standardization and offers real-time updates for managers and supervisors, who can further streamline their lockout/tagout procedures.
Furthermore, the free 30-day trial of resco.Inspections comes with a free OSH risk template that you can easily customize for LOTO scenarios as well.
Violations
If you violate LOTO standards, there is a penalty that you must pay, so beware of these most common lockout tagout violations:
- Failing to classify and cut off all energy sources
- Failing to shut down the equipment
- Not capable to de-energize
- Incapable to drain residual energy
- Unable to establish a lockout tagout program
- Incompetent of developing and enforcing a lock out tag out policy
… and many others.
Responsibilities
In a work setting, each individual is responsible for the lockout/tagout program.
Management
From drafting to updating lockouts, management is responsible for handling all these procedures. Along with that, they are also involved in identifying employees, machineries, equipment and all other processes involved in the program.
Supervisor
Supervisors are accountable for distributing protective equipment, hardware, and any appliance, along with ensuring employees properly use them.
In addition, they are also involved in ensuring that equipment-specific procedures are established for the machines, equipment and processes in their area.
Lastly, they must make it certain that the employees are strictly following the lockout procedures where required.
Authorized Individual
Authorized individuals are required to follow the developed procedures and report any problem associated with those procedures.
Starting with a LOTO program
OSHA standards help to prevent injuries and deaths occurring in the workplace. By developing good lockout/tagout procedures and following protocols, companies can ensure employee safety and government rules compliance.
If you are just starting with LOTO, make sure to follow the latest recommendations and guidelines from OSHA. And whether you’re just implementing or already running a LOTO program, check out resco.Inspections to achieve further standardization and streamlining of your procedures.
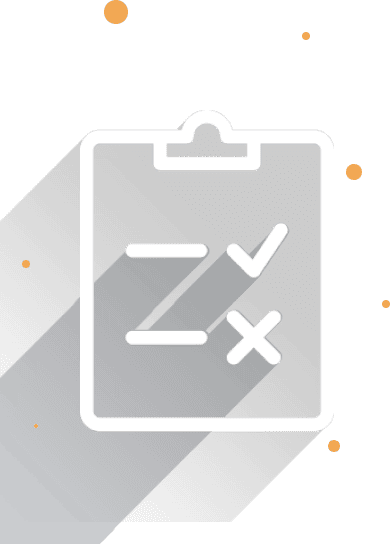
Possible Hazards Checklist
Download a free Possible Hazards Checklist template to significantly improve your workers’ safety by completing the hazard scans