A recent Microsoft survey indicates that 65% of frontline workers view artificial intelligence as a tool that can alleviate their workload and amplify their contributions. This points toward a future where AI seamlessly augments human impact.
The collaboration between Resco and Microsoft is a testament to such digital integration’s power.
Previously, we explored how the fusion of Resco and Azure Custom Vision’s AI digitized health and safety processes in the construction and oil & gas industry.
Now, let’s shift our focus from safety inspections to field service and equipment recognition.
The use case: Equipment recognition in field service
Efficient equipment recognition is a critical aspect of field service operations.
Technicians need to identify and validate various equipment pieces swiftly and accurately, whether for maintenance, repair, or replacement purposes.
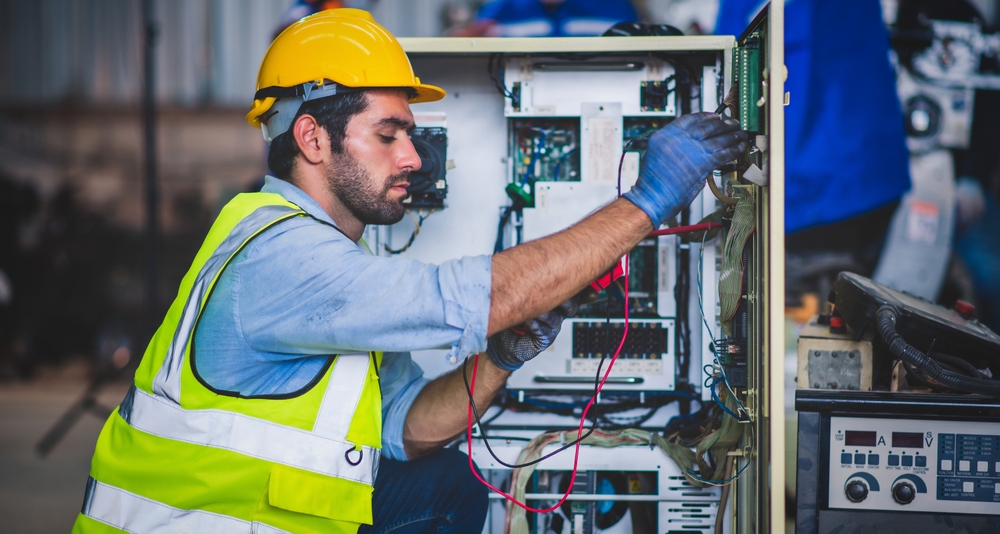
This process often relies on manual documentation or memory, leading to potential errors and delays. But now you can combine Resco (including the new Power Platform solutions) and Azure Custom Vision to create a faster and more comfortable solution for frontline workers.
The solution: Smart forms and AI working together
Field technicians can employ mobile forms in Resco Inspections+ or the newly announced Resco Forms+ to capture images and details of equipment on-site, creating a comprehensive visual database.
This solution enables inspectors to collect and evaluate data digitally. Technicians can fill out information about work progress or create reports without needing to rewrite data or use desktop devices.
All data is synced with the core databases of organizations thanks to native integration with Microsoft’s platforms and data management tools, including Dynamics 365, Power Platform, and Dataverse.
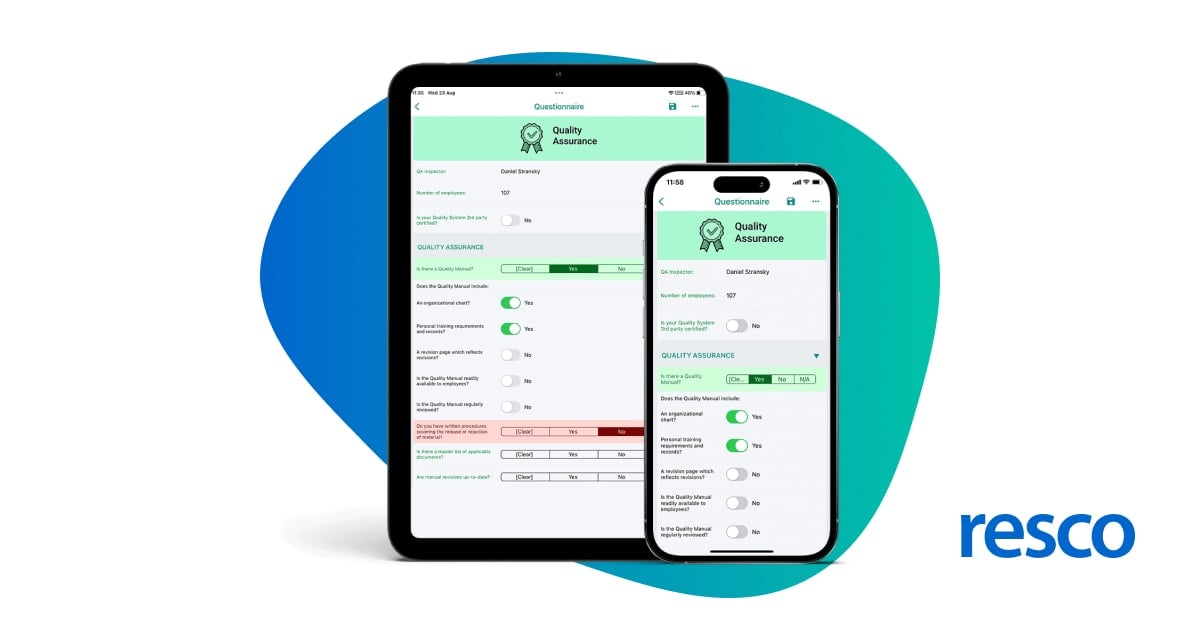
Integrating Azure Custom Vision’s AI empowers workers to automatically identify and classify equipment, eliminating the guesswork and significantly enhancing efficiency.
For example, if they find a defective part, they can easily document it with a photo and quickly secure a replacement. No time is wasted searching for the correct part, as the system performs this task automatically.
This technology can also be used for other questions, like looking up items in a product list. If the captured image matches a tag in the pre-trained model, it becomes the answer. This saves time and ensures accuracy in various field service tasks.
Technical integration: Synergy of Resco and Azure Custom Vision
Let’s assume you’ve already pre-trained your Custom Vision model for the image recognition of various spare parts typical for your industry.
Accordingly, you’ve also established a link between this model and your mobile project in Woodford. You’ve also created an existing questionnaire template used during technician visits to monitor assets (e.g., elevators in our case). If not, find the steps to do this in our documentation.
Now, let’s find out how to leverage custom vision to identify and find a missing part in a lookup view.
Imagine that during your site visit, you find out that some parts are subject to corrosion. You must photo-document the defects and simultaneously secure the supply of new spare parts.
Compliance with all technical prerequisites and picking up the proper production types and models are mandatory. You’re already capturing the defective part, why not speed up the process?
Use the “image recognition” question format in Questionnaire Designer to capture the spare part. If the captured image matches a tag in the pre-trained model, the tag’s name becomes the output answer.
This outcome may be applied to other questions as well, such as a lookup question pointing to the product list in our case.
If there exists any product with the name matching the recognized tag, the lookup is automatically filled in with detected part. No other data input from the technician operative is necessary.
Why it matters
Operational agility: Instant recognition optimizes equipment-related tasks, enabling technicians to take informed actions.
Enhanced productivity: Real-time evaluation and automatic recognition saves time for field technicians, boosting overall efficiency. At the same time, it saves them a mental capacity needed for remembering or finding the correct equipment.
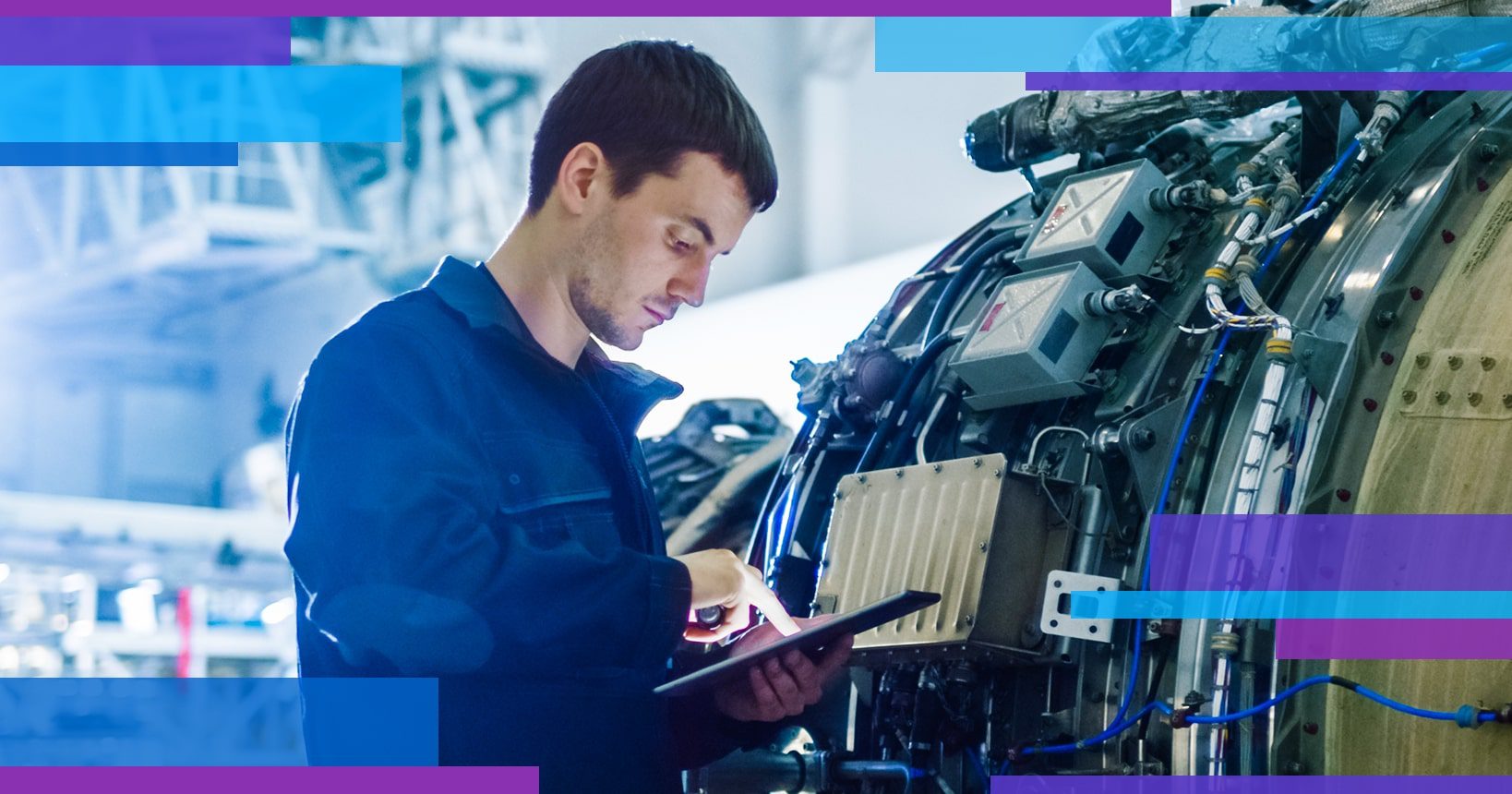
Compliance and records: Digital data collection, paired with visual documentation, strengthens data integrity and regulatory compliance for field service organizations.
Code-free integration: The native integration with Microsoft platforms and no-code development enables IT teams, consultants, and partners to seamlessly leverage digital forms and AI’s advantages without spending resources on coding and maintenance.
Conclusion: AI as the booster of efficiency
The solution combining Resco and AI enables technicians to scan and recognize equipment efficiently through image recognition, bridging the gap between the physical and digital realms.
This capability not only accelerates workflow but also ensures accuracy and consistency in equipment identification.
But the combination of AI recognition and mobile forms isn’t just limited to equipment recognition.
It can be an accelerator of processes in various fields:
Inventory management: To streamline retail and warehouse operations by scanning and cataloging products accurately, reducing errors, and optimizing restocking processes.
Quality control: Enhance quality assessments in manufacturing by automatically identifying and categorizing product defects, increasing accuracy.
Retail and e-commerce: Simplify product searches for shoppers by allowing image-based product identification, making the shopping experience more efficient.
Healthcare: To improve patient data capture and medical image tagging for healthcare professionals, simplifying data retrieval and analysis.
If you’re intrigued by the prospects of integrating Microsoft business apps with Resco mobility, reach out for more information.